The Centre for Advanced Low-Carbon Propulsion Systems (C-ALPS) at Coventry University houses some of the UK’s most advanced technologies for testing sustainable power concepts for cars, airplanes and other modes of transport. The centre is a world-leading pioneer in developing next generation power trains for cleaner transport. Fireworks designed and installed the fire protection system for C-ALPS’ testing cells and communications offices.
Overcoming fire risk factors for powertrain test cells
C-ALPS incorporates five state-of-the-art powertrain test cells. Here, researchers and engineers work to test systems to their maximum capacities. Their goal is to improve performance and emissions on a range of hybridized, electric, conventional and alternative fuel-based powertrain concepts. High power outputs, combustibles and machinery running at high temperatures all contribute to risk factors for fire outbreaks. Personnel and high-value equipment need the most performant fire protection in this environment.
Fireworks’ engineered solution for C-ALPS is designed to deliver the fastest fire, smoke and heat suppression in the event of fire. The high pressure watermist system created by Fireworks offers the greatest possible protection for staff and is safe to use with combustibles. As only very small amounts of water are used in the event of fire, it does not interfere with the smooth running of data equipment and normal operations can be resumed quickly.
A complete fire protection system
C-ALP’s engine test cells and communications room have each been equipped with heat and flame detectors for automatic fire protection. These detectors are linked to fire-extinguishing control panels, which can also be operated manually. In the event of fire, a signal is sent to trigger the operation of a compact but powerful watermist pump. To ensure maximum reliability, water can be sourced from the purpose-built storage tank, or the mains water supply.
A network of 316-grade stainless steel pipework and valves connect the pumps to the watermist nozzles located in each of the test cells and communications room. Depending on the configuration of each area, some watermist nozzles are located at high-level, while others have been fitted under the perforated grill floor.
How watermist works
Upon activation of the system, water is pumped through the pipe network at high pressure and is discharged as atomised water droplets (watermist) through the nozzles in the affected area. The small size of these droplets makes them airborne, drawing them directly to the source of the fire and capturing smoke particles. Watermist, due to its high surface area to volume ratio, has unrivalled cooling and fire suppression capabilities.
Special requirements
One of the challenges for Fireworks to overcome at C-ALPS, is that the site has minimal power available to run the watermist system. The solution provided by Fireworks, with the use of a frequency converter, offer one of the lowest electrical current requirements on the market. Fireworks also incorporated an Uninterrupted Power Supply (UPS) into the watermist pumps, to provide the system with a standalone minimum run time of 10 minutes, as per the latest British Standard 8489.
Installation was carried out by Fireworks’ experienced team of engineers, with full adherence to the recommendations laid out in the NFPA 750 code of practice. Fireworks also carried out pressure testing and commissioned the system.
Other Fireworks’ services include regular, scheduled maintenance and a 24/7 call out service.
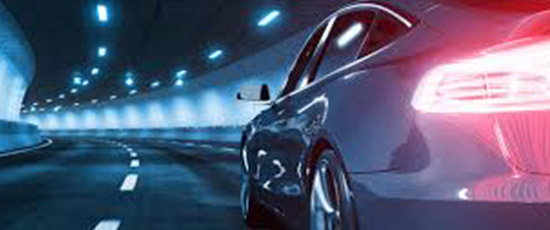
Related Topics
Case study – Institute for Advanced Automotive Propulsion Systems
Book your free, Institute of Fire Enginneers-accredited CPD session on Understanding Watermist Fire Suppression.